Have you ever wondered how Taipan are able to ensure our matched systems of hose and hose tails are able to meet or exceed manufacturing standards?
These internationally recognised standards govern some pretty important things, including the tolerance of inside diameter, outside diameter, cover thickness, over wire dimension and bend radius of hydraulic hose, as well as specifying the working pressure rating and burst pressure rating of the hose.
For those who’d prefer it in simple terms, these standards specify how each hose should be made and how it should perform. Taipan guarantees that all our hose assemblies meet or exceed these standards by undertaking rigorous impulse testing.
But what is impulse testing?
Impulse testing is the process of testing unaged hydraulic hose assemblies up to the standard they are manufactured. This allows us to establish a matched system of hose and hose tails. At Taipan, the method we use to test our hydraulic hose uses ISO 6803, Impulse Testing without flex.
Before we can get started on an impulse test though, a few key things must be checked.
Firstly, the manufacturer of the hose will publish a specification sheet, which gives us the dimensions and ratings of all those important things mentioned earlier. From this, we can go back and reference the standard the hose has been manufactured to and confirm the hose dimensions. This is very important, as a lot of the calculations we need to do are based off these measurements. Being even a few millimetres off can mean the difference between a pass or fail! (Or the difference between a good matched system and a shoddy one).
Once we are satisfied with the qualification checks, we move onto the calculations. Unfortunately, we don’t have the time in this article to go over all the math (what a shame!), but we have included a couple of the formulas we use below, to give you an idea of how much thought goes into getting the product ready for impulse testing.
The free length hose for a 180-degree test is calculated using the following formula:
π(R+D/2) + 2D (with a tolerance of + 1% or + 8mm – whichever is greater).
The calculation for the distance between centres is the following:
2R + D (with tolerance of + 5% – 0%)
R = Radius
D = Hose Outside Diameter
As you can see, it’s an exact process!
Here at Taipan, it is vital that we perform these qualification checks of the hose, as this ensures we conform to the correct parameters of the standard.
The final step before impulse testing is to establish a crimp dimension. The method to this varies based on manufacturer, so we adjust and crimp accordingly. A mandrel is often used to check each crimp until the point of tail collapse is achieved.
Then comes the cool part. It’s time to impulse!
To do this, the hose assemblies are fitted to the Bimal Test Stand, a world recognised machine capable of testing our complete range of hose. Once installed, the test is set up based on the parameters outlined in the relevant standard. Percentage of working pressure, number of cycles and temperature of test are all specified using manufacture standard. Hydraulic hose is usually tested to 120% – 133% of working pressure for 150,000 – 500,000 cycles, at a temperature of 100 – 120 degrees depending on the applicable standard.
The tester impulses the hoses at a rate of 1hz at the nominated pressure, cycles, and temperature. This means that every single second of the test time, the hose assemblies are pulsed to the specified pressure for the life of the test. In a matter of days, the impulse tester can show us information that would have taken months or even years to receive in a real-world scenario!
An impulse test provides an ability for Taipan to establish a matched system. We impulse test all our hose assemblies with an above normal set of conditions, to ensure we are selling a product we are confident will meet the demands and expectations of our customers. If you would like any more information on our impulse testing, give our friendly team a call on 1300 654 782.
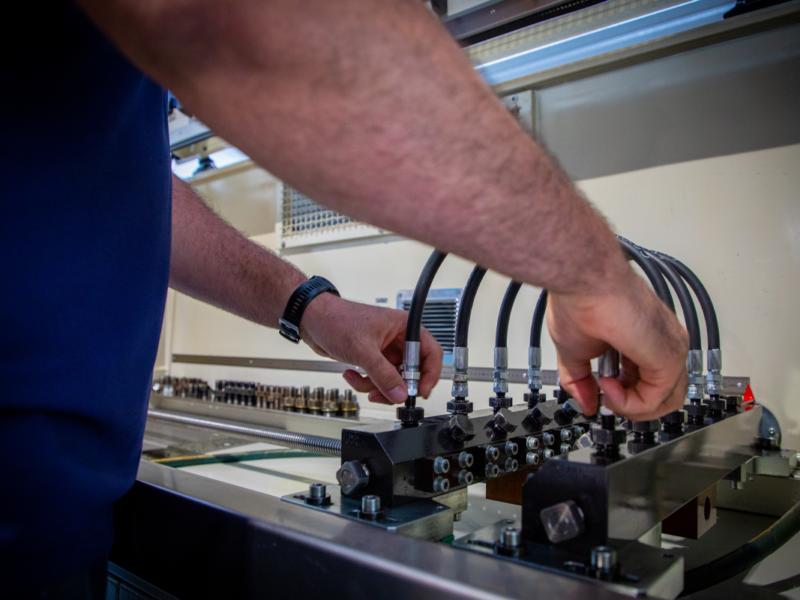